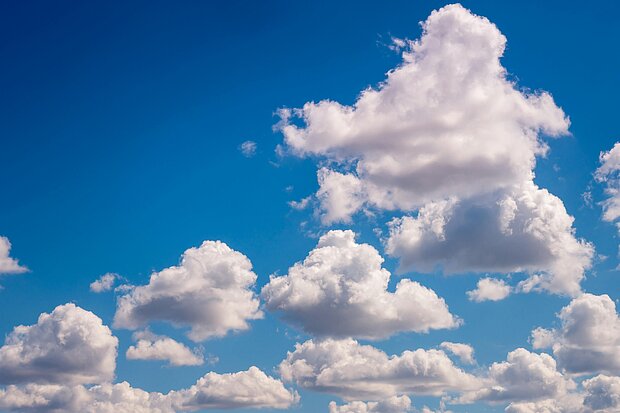
AndonCloud
AndonCloud reduces downtime and streamlines the flow of information for a manufacturing plant. It also helps save money by minimising the delay between changing the status of the machine and calling the appropriate services for repair.
Industry: Production
Customer: An American conglomerate
The American conglomerate, which has a strong presence in machine and plant production, energy generation and the oil industry, is one of the largest companies in the world. The company entered the Polish market in the 1990s and today operates eight production plants employing 7,300 people. Our customer is a plant for the production of generators.